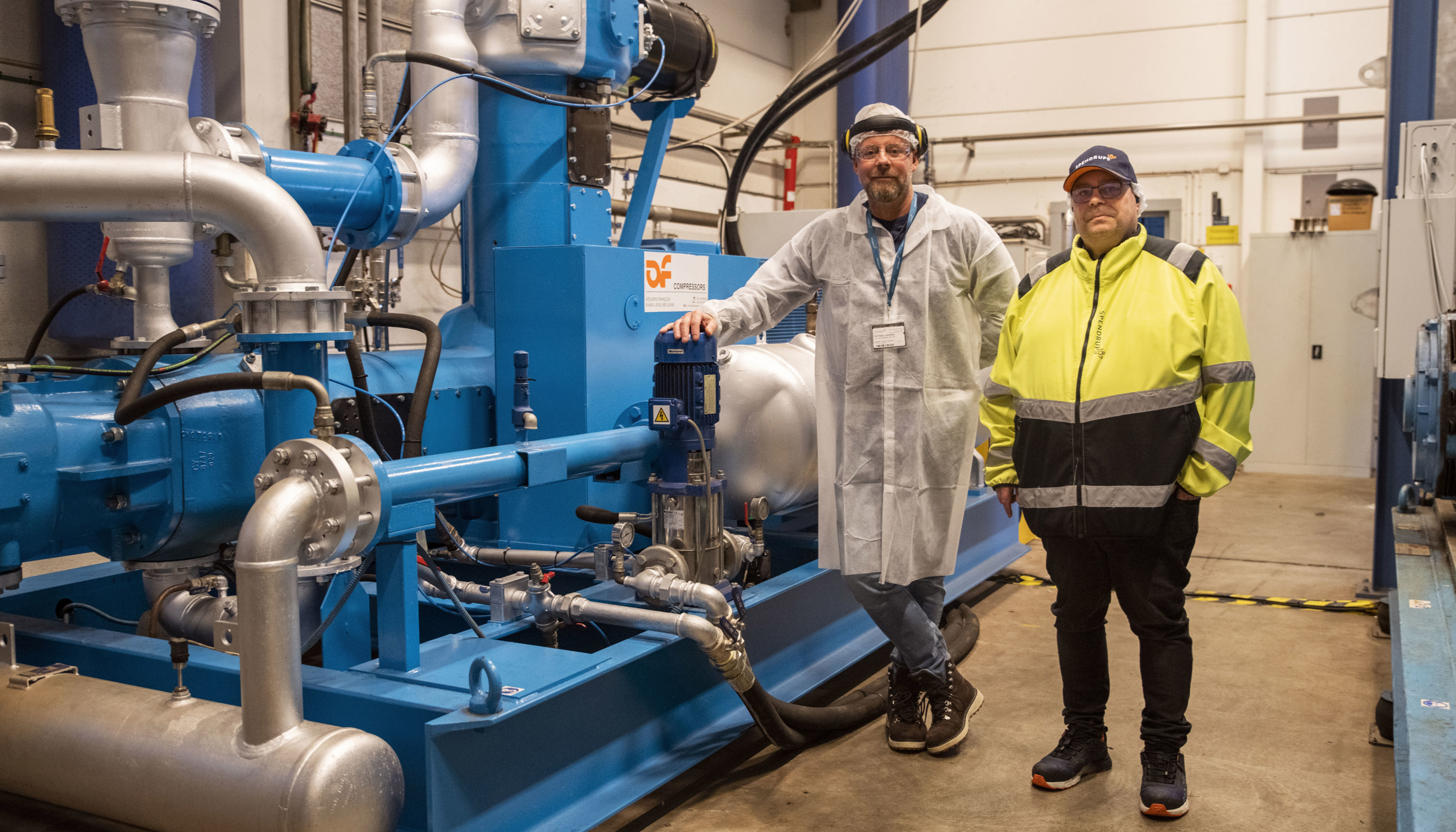
Solutions that save energy for brewery giant
The Instalco company, Kompressorteknik has been engaged for energy efficiency work at Spendrup’s brewery in Grängesberg. Through innovative product solutions, Kompressorteknik has captured savings for Spendrups. Not only have the energy costs decreased, but there is now also a higher level of utilisation.
Kompressorteknik in Ludvika specialises in refining compressors that have reached a certain age. It purchases used compressors to then disassemble them and renovate the various parts. Once the compressor is reassembled, it is essentially new, with nearly the same warranty of service life that it had when newly purchased.
Spendrups uses compressors to inflate PET bottles, which are later used in production. It is step one in a chain of production used at the brewery.
“Compressors are the source of the single largest energy consumption at the brewery,” explains Mathias Lindgren, Founder and CEO of Kompressorteknik.
Spendrups has the stated goal of focusing on improvement efforts for higher energy efficiency.
“The savings have come about through lower energy consumption by having increased the level of utilisation, along with sustainability benefits in the form of longer service intervals,” says Patrik Gustafsson, Operations Manager at Spendrups.
Mathias Lindgren highlights two distinct improvements revolving around energy efficiency that his company has captured for Spendrups.
“Our solutions have enabled Spendrups to transition from a static, hourly based service interval of 2,000 hours to longer, permit-based maintenance of around 3,000 hours using a machine monitoring system. Spendrups has also increased its utilisation level from 30 to more than 60 percent,” says Mathias Lindgren.
Kompressorteknik’s solutions also reduce Spendrup’s environmental impact in that the need for oil changes and replacement parts in the compressors has decreased.
“If this isn’t sustainability, I don’t know what is,” says Mathias Lindgren.
And, Spendrups has embraced his idea of reusing the large compressor after a complete overhaul and they invested in three smaller compressors instead.